With gusto, Warwick started building the Burrell Traction engine back in 2016. Warwick’s first task was to build a 3D printer to create prints replicating the engine parts. When looking to turn the 3D prints into castings, a friend referred Warwick to Steve Read from Read Industrial.”
“It’s always fascinating to see the project come to life piece by piece.
Our client’s dedication: including the time, effort, and costs involved, can be considerable. We are lucky to be able to enjoy and admire the finished work. Warwick’s legacy project will certainly be admired by Traction engine enthusiasts many for years to come.” Says Steve Read – Factory Manager “Read Industrial.”
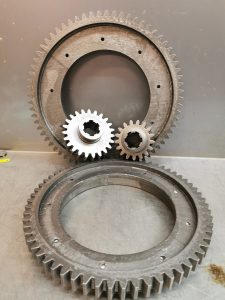
The traction engine gears are lost-cast in SG iron using 3D prints.
continued ….
Read Industrials investment foundry draws in clients with a diverse range of projects. The foundry team takes pride in gaining an understanding of the client’s inspiration. Furthermore, the team discuss the casting’s end-use to determine the best method to be applied. In this case, using the lost wax process allowed our foundry team to achieve intricate detail. The traction engine gears are lost-cast in SG iron using Warwick’s 3D prints. Over time Reads lost wax foundry has completed most of the axel tubing, the wheel hubs, and all sorts of replica componentry for the Burrell.
Warwick describes his traction engine build as his earthquake stress project. Being a project of passion, Warwick is quick to say that his finish date could be this Christmas or perhaps the next. Warwick’s nostalgic Burrell traction engine has only a few parts to complete before its finish, including two water pumps and clack valves.
Want to find out more about our lost-wax foundry? or more importantly, what we can do for you?