Welding
Welding metals is an art form in itself
Weld joints always need three things: strength, resistance to corrosion, and surface finish. Usually, in that order of priority. Our team of experts can guarantee all three, if required.
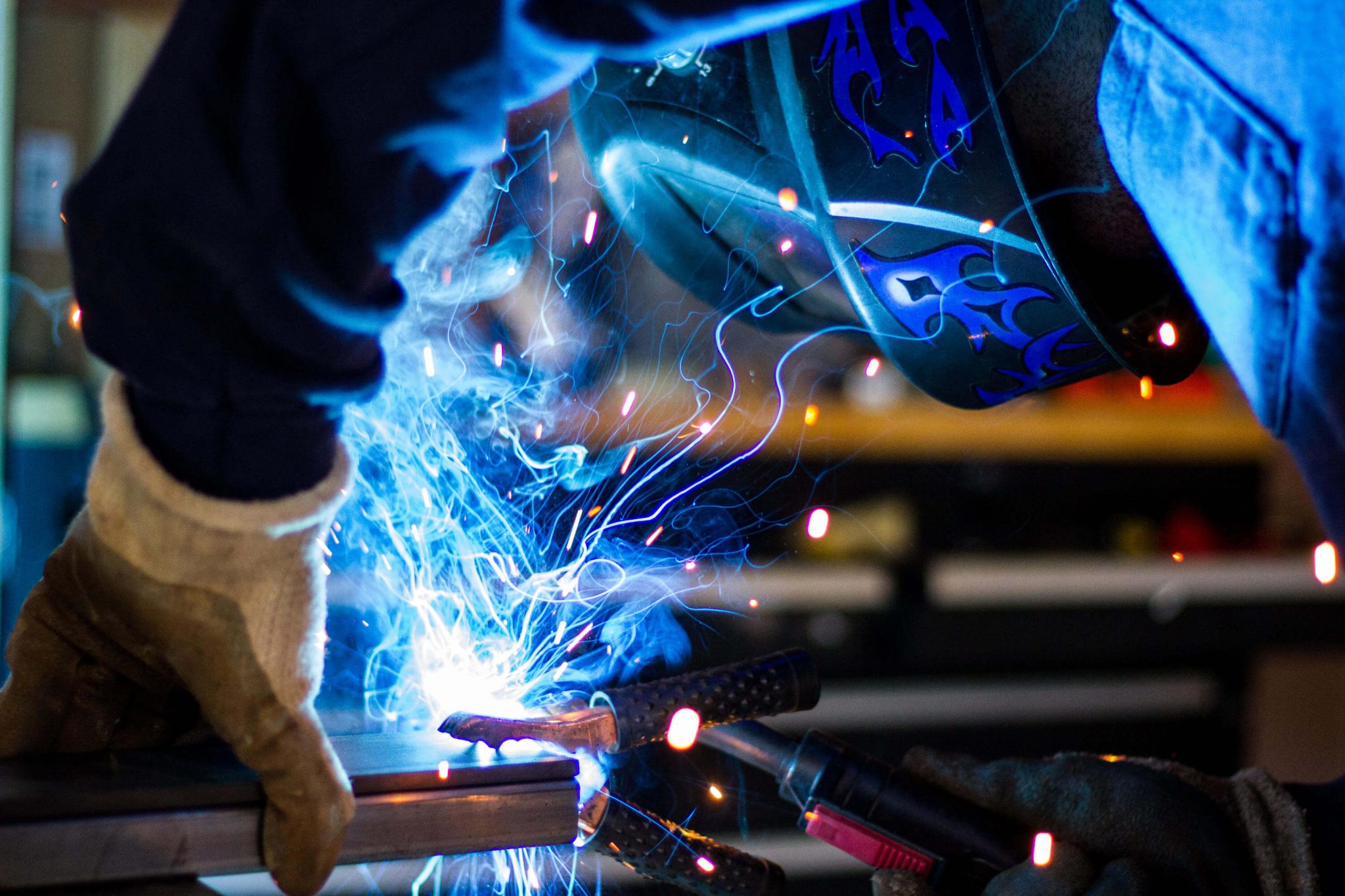
Welding processes
We have equipment for fusing ferrous metals such as steel and stainless steel, and non-ferrous metals such as aluminium. Our welders are certified to the AS/NZS2980 standard for MIG in flat, horizontal, vertical and overhead positions. We use:
-
MIG, using either gas or flux core wire. MIG is usually the quickest and most common welding process we use for steel and aluminium.
-
TIG, generally we use this for aluminium or stainless steel sheet metal fabrication to achieve a high degree of surface finish. For example, on vat units and water reservoirs. It’s the most time consuming, but it’s the only method that can produce a neat weld joint on stainless steel.
-
ARC, we tend to use MIG in place of ARC unless there is a need for deep penetration. For example on heavy machinery or structural steel.
-
Oxyacetylene, useful for fusing mild steel and bronze, and for fusing metals using brazing.
No matter the method, if the final finish needs to be of a high standard, strong, and able to resist corrosion, then we guarantee it.